Le Zamak et la résistance à la corrosion
L’alliage Zamak étant principalement composé de zinc (95%), il offre une tenue correcte face à l’oxydation en milieu abrité, mais exposé aux intempéries et surtout au contact d’une ambiance saline un phénomène de rouille blanche peut rapidement apparaitre. Celui-ci est empirique, à la manière d’une rouille rouge affectant les aciers.
Dans la plupart des cas la pièce va se ternir et si l’ambiance est agressive une poudre blanche (l’oxyde de zinc) va se former et venir attaquer sa surface. Le processus peut s’étaler sur plusieurs années voir décennies avant une destruction totale si la pièce est exposée et non-protégée, le cas le plus défavorable étant en bord de mer, non abritée.
Utilisation de lubrifiants au contact d’une pièce brute (sans revêtement de surfaces) :
- Les lubrifiants ne doivent pas contenir de produits d’origine animale ou végétale qui, en se décomposant sous l’effet du temps, formeraient un produit acide risquant d’attaquer le zamak. Les lubrifiants d’origine minérale, comme la plupart des huiles, ne présentent pas ce risque.
Afin de se prémunir du phénomène une gamme de revêtements techniques est disponible, chacun présentant leurs avantages et inconvénients (résistance, prix, aspect etc..).
Pour mesurer la résistance à la corrosion, un test de vieillissement accéléré est réalisé dans une étuve : le test B.S. (Brouillard Salin).
Les tenues des revêtements sont exprimées en Heures au test de brouillard salin.
-
Le zingage :
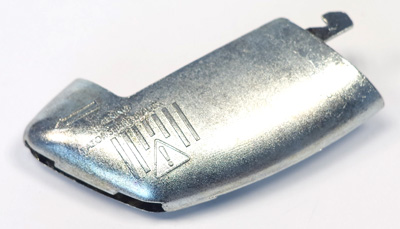
La protection la plus courante est le zingage qui consiste à déposer une fine couche de zinc pur (inf. à 0.01mm) à la surface de la pièce par électrodéposition.
le zingage se réalise principalement en vrac en remplissant les tambours de pièces qui seront immergées dans les différents bains du process.
L’opération est également possible au bain mort/à l’attache pour les pièces plus volumineuses.
Il est réalisé selon la norme NF A 91-102 « Revêtements métalliques – Dépôts électrolytiques de zinc »
Revêtements par zingage électrolytique sur zamak | ||||
Noir | Blanc standard | Blanc renforcé (HTBS) | Renforcé + filmogène | |
Aspect | noir-brun, irisé | peu irisé | irisé bleu | irisé bleu |
Tenue BS Max. | 48h | 96h | 120h | 240h |
Coût | + | – | + | ++ |
-
La passivation :
Le procédé de passivation est traitement chimique par aspersion ou trempage qui provoque au séchage un mélange de chromate de zinc et d’hydroxydes qui seront partiellement déshydratés conférant à la pièce sa protection, l’épaisseur déposée est proche du micromètre et d’aspect gris clair irisé.
Dans le cas de pièces peintes, pour renforcer la tenue B.S. une passivation aura également l’avantage de favoriser la tenue de la peinture.
La passivation avant peinture est même recommandée sur des pièces qui risquent d’être exposées à l’humidité et particulièrement à une atmosphère tropicale.
A elle seule la passivation apporte une tenue B.S. moyenne de 72h et dans quelques cas jusqu’à 200h qui peut servir de protection temporaire pour du stockage de longue durée.